CASE STUDIES
FANO
Modernizes workflows, gains robust
functionality across departments
The Query
FANO wants a modern, updated system that automates processes, connects and integrates, provides oversight of all departments.
FANO is a family owned label printing and flexible packaging company that has been in the printing industry market since 1995, when it was an offset printer. Since then, FANO’s successes led them to greatly expand their services–adding labels and packaging to their commercial printing business. Today, FANO provides self-adhesive labels, flexible packaging, shrink sleeves, stationery, folding, stamping, laminates, embossing and roll-to-roll films to its customers.
FANO grappled with a range of operational challenges stemming from their reliance on simple, non-integrated systems. The lack of integration, manual processes, limited functionality, and inadequate financial oversight placed Fano at a constant disadvantage. These challenges underscored the need for a comprehensive ERP/MIS solution that could seamlessly link all aspects of their business operations, from estimating and planning to production and financial management
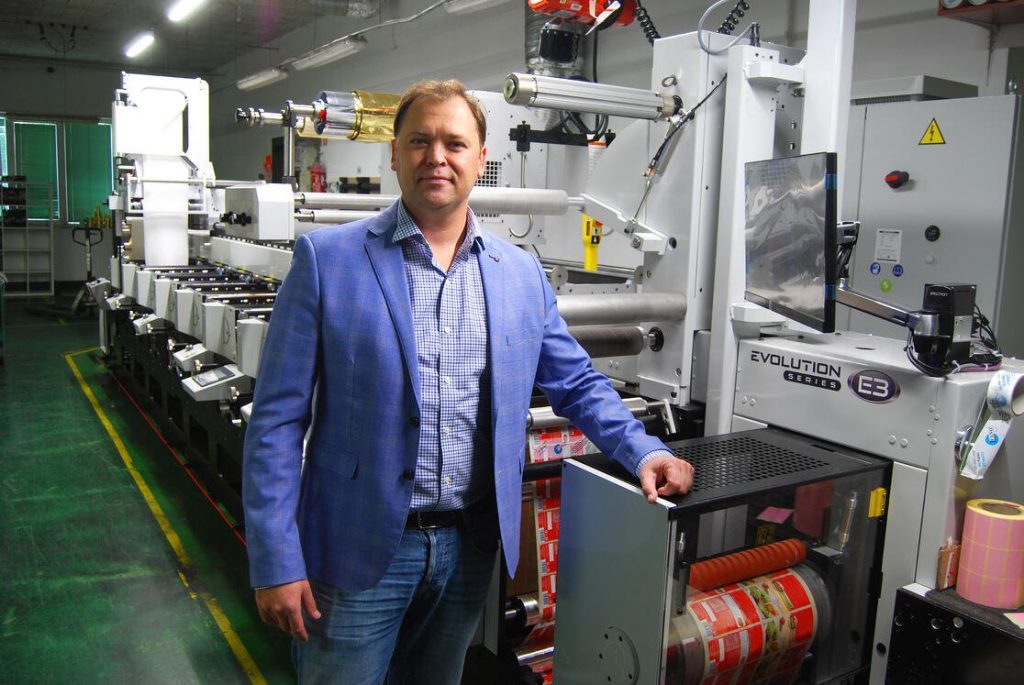
PRODUCTS
Folding carton, sleeves, trays, barrier coatings
MACHINES
Nilpeter 6 color flexo press, Epson
4900, laminators, folder/gluers
COMPANY size:
90 + employees
Location:
Warsaw, Poland
The challenge
Excel spreadsheet based management and a lack of integration posed problems for the growing company.
At the inception of their business, Fano Packaging faced significant operational challenges due to their reliance on simple Excel spreadsheets. This approach, while initially manageable, quickly became a bottleneck as the company grew. Excel spreadsheets were used for various tasks, including calculations, pricing, and creating basic scheduling plans. However, this method was far from efficient and posed many critical issues:
1. Lack of Integration:
The spreadsheets were standalone files that did not communicate with each other or with other essential systems. This lack of integration meant that data had to be manually transferred between sheets, increasing the risk of errors and inconsistencies.
2. Manual Data Entry and Error-Prone Processes:
Relying on manual data entry was not only time-consuming but also prone to mistakes. Even minor errors in data entry could lead to significant issues in pricing, scheduling, and overall project management.
3. Limited Functionality:
The basic Excel system provided minimal functionality, covering only the essentials of calculations, pricing, and simple scheduling. There were no advanced features for comprehensive production planning, real-time monitoring, or detailed financial analysis.
4. Absence of Comprehensive Modules:
The system lacked modules for production, financial management, and post-production analysis. This absence meant that Fano could not track production metrics in real-time, analyze financial data comprehensively, or assess post-production performance effectively.
5. Operational Challenges:
The lack of an integrated system meant that Fano was unable to streamline their operations, resulting in inefficiencies and a reactive approach to problem-solving rather than a proactive one. As Bolesław Jasinowicz, Fano’s vice president, stated, “We were constantly working at a disadvantage.”
6. Disjointed Workflow:
Without a unified system, different departments within Fano operated in silos. This disjointed workflow caused delays and miscommunications, making it difficult to maintain consistent quality and meet production deadlines.
7. Inadequate Financial Oversight:
The absence of integration with financial and accounting programs meant that financial oversight was severely lacking. Fano struggled with delayed invoicing, inaccurate cost tracking, and an overall lack of financial visibility, hindering their ability to make informed business decisions.
“The number of errors in our company has certainly decreased. By automating processes, defining the various work parameters in the system, we have made significant progress in this respect.
The solution
FANO recieves operational efficiency and visibility across the organization.
Fano Packaging faced several challenges with their previous system, including a lack of transparency, difficulty in accessing real-time data, and inefficiencies in linking various business processes. With the implementation of HiFlow, these challenges have been effectively addressed, resulting in a significant transformation in their operational efficiency and workflow management.
One of the standout features of HiFlow for Fano is its user-friendly, multi-window interface. Unlike their previous system, HiFlow’s interface is designed to be intuitive and accessible, allowing users to navigate seamlessly between different functions and modules. This transparency ensures that all stakeholders, from management to shop
floor operators, have instant access to the information they need at various levels of detail. This real-time access to data empowers employees to make informed decisions quickly, enhancing overall productivity.
The system suggests solutions, prevents mistakes, and facilitates FANO’s workflow. And by integrating all information into a single database, the system enables efficient day-to day process control, optimizing production. For example, the rapid startup of product workflow translates into production repeatability, which translates into cost savings. Estimating, quote, product order–all produce shop floor data that is accurate and timely.
HiFlow’s capabilities extend to the production floor, where real-time data collection is essential for monitoring performance and efficiency. The system captures data directly
from machines and other production equipment, providing insights into machine utilization, labor productivity, and overall production performance. This real-time visibility allows Fano to identify bottlenecks and inefficiencies promptly, enabling them to implement corrective actions swiftly and maintain high production standards.
HiFlow’s capabilities extend to the production floor, where real-time data collection is essential for monitoring performance and efficiency. The system captures data directly from machines and other production equipment, providing insights into machine utilization, labor productivity, and overall production performance. This real-time visibility allows Fano to identify bottlenecks and inefficiencies promptly, enabling them to implement corrective actions swiftly and maintain high production standards.
“I love the modern business intelligence provided by the system. It gives us unrestricted access to information in real time and offers us the possibility of making faster and more optimal decisions.”
Takeaways
Systematic Linking of Essential Documents in One Database
HiFlow integrates key business documents such as calculations, estimates, quotes, production plans, and more into one central database. This integration ensures that all stages of the business process, from estimating and planning to scheduling, production, and invoicing, are connected seamlessly. The result is a smooth and flawless workflow, minimizing errors and reducing the time spent on manual data entry and reconciliation.
Comprehensive Integration with Invoicing
The benefits of HiFlow are also evident in the invoicing process. By linking production data with financial systems, HiFlow ensures that invoicing is accurate and timely. This integration eliminates the discrepancies that often arise from manual data transfers and ensures that all billing information is up-to-date and reflective of actual production activities. For Fano, this means faster, more accurate invoicing, improved cash flow, and enhanced financial management.
Enhanced Estimating and Planning
With HiFlow, Fano has seen significant improvements in their estimating and planning processes. The system’s robust tools allow for precise calculations and detailed estimates, which are crucial for accurate project planning and cost management. By linking these estimates directly to production plans, scheduling and warehouse, HiFlow ensures that all departments are aligned and working towards common goals, reducing the risk of miscommunication and delays.
The Benefits of Partnering
with HiFlow Solutions
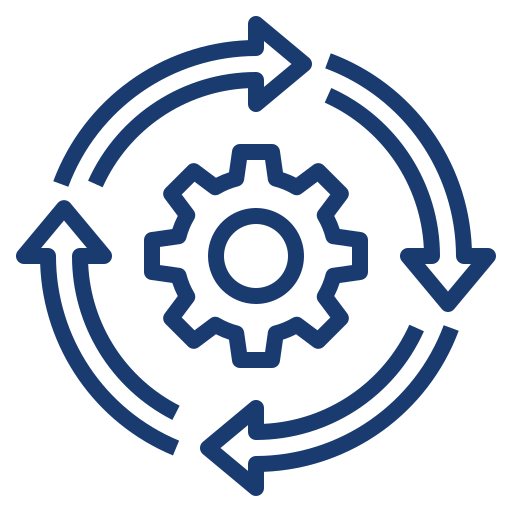
We implement – fast. The HiFlow system combines MIS and MES software with easy ERP integration.

We fill your ERP gaps. By optimizing ERP systems with MIS and MES features required for packaging and label printing.
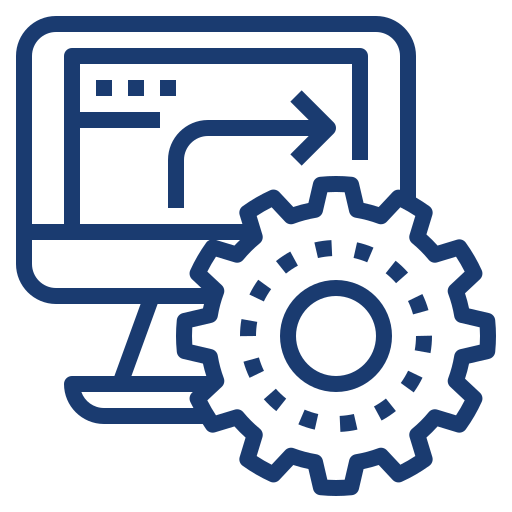
We create automated environments. With seamless connections from order intake to shipping and invoicing.
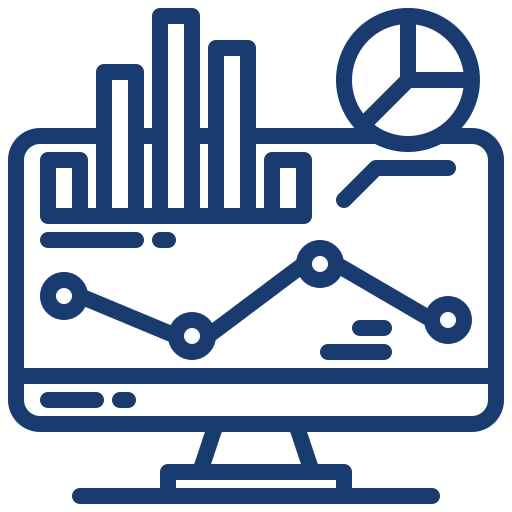
We feed you data. With insights from real time, critical information from your production shop floor, personnel, and equipment.
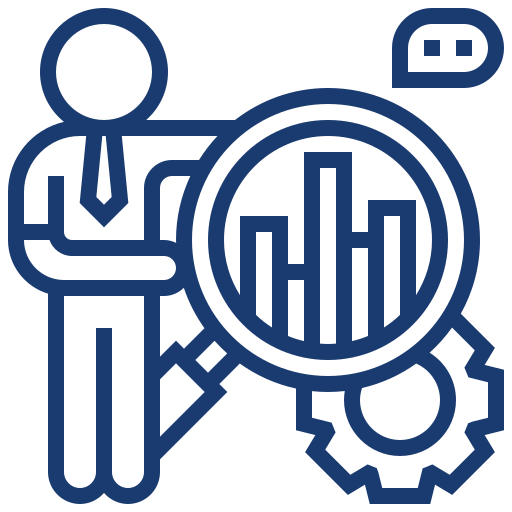
We let you see. From smart scheduling to nested layouts to workflow diagrams, instantly see where you stand within the job.