CASE STUDIES
BADGER PAPERBOARD
Synchronizes its multiple locations; increases productivity and efficiency
The Query
Paperboard manufacturer needs comprehensive system that connects across multiple locations.
Badger Paperboard is a custom paperboard converter specializing in packaging and shipping materials. With more than 30 years in the industry, Badger has 4 locations across the US in Wisconsin, North Carolina, California and Texas.
“Our goal was to manage the entire process seamlessly—from request for quote and order processing, to production planning, shipments, and invoicing,” states Jacob Smiley, President of Badger. “A key objective was to connect all our plants under one platform with a unified database, enabling us to manage operations from a single location while accounting for time zone differences across our sites. We needed a robust ERP/MIS that could serve as a single source of truth and the system of record for all our locations.”
PRODUCTS
Paperboard sheets, chipboard pads, corner guards, fanfold corrugated cardboard
MACHINES
Sheeter, stripper, die cutter, corner machine, laminator
LocationS:
Freedonia, WI
La Mirada, CA
Houston, TX
Belmont, NC
The challenge
Legacy software and disconnected locations was holding back a growing company.
At Badger, we were operating on legacy software that had become a significant barrier to our growth. The software was no longer supported, which not only left us without reliable technical assistance but also restricted our ability to scale and modernize our operations. This outdated system lacked the flexibility and functionality we needed to keep pace with the demands of our industry.
One of our critical needs was for a comprehensive estimating system that could produce precise cost calculations, essential for maintaining competitive pricing and profitability. Additionally, we were looking for automated scheduling and tracking of material consumption to enhance efficiency and reduce manual errors. Overall, we required a cutting-edge solution capable of automating our processes from end to end, adding speed and efficiency to our shop floor operations.
With four plants spread across the United States, one of which was newly opened, we also faced the challenge of integrating these multiple locations operationally. Previously, our four locations were set up as mostly independent systems. Although they were connected, each plant operated with its own management system, leading to frustrating lag times between facilities. This disjointed setup made it difficult for staff to coordinate effectively and hampered our ability to manage operations seamlessly across the entire organization.
We needed to implement an overarching MIS/ERP solution across all four locations, standardizing the data infrastructure, adding automation, and synchronizing operations across the entire organization. That means that owners and managers can quickly and easily put their hands on the exact data and information they are seeking, whether it be business/financial, prepress, production, customer engagement, inventory and warehousing.

The solution
Integration across multiple locations, automation of processes and robust data collection.
From the outset, HiFlow demonstrated a commitment to clear communication and tailored solutions. During the initial meetings, every inquiry was meticulously addressed with tangible examples from the sandbox database. This dynamic tool, continuously updated with configurations specific to our machines, materials, and workflows, proved invaluable. HiFlow’s decision to maintain a live, evolving sandbox environment meant that we could visualize and interact with the system in a way that was directly relevant to our operations. Weekly meetings were set up by HiFlow to ensure that both teams remained aligned and the project stayed on track. These sessions were not only vital for real-time updates but also served as a platform for problem-solving, addressing questions, and making necessary adjustments based on our team’s availability and production schedules.
One of the primary challenges we faced was the inefficiency of using disparate tools that did not communicate with each other. HiFlow’s solution was to integrate all these tools into a single, unified system interface. A significant improvement was replacing our external estimating system with HiFlow’s comprehensive Estimating modules.
These modules are linked in real-time to critical areas such as inventory, die and tool availability, scheduling, and purchasing. This integration has streamlined our operations, reduced manual errors, and significantly improved our ability to manage resources effectively.
The implementation strategy began with the launch of the solution at our first location in North Carolina, which was still under construction at the time. Despite the challenges posed by the ongoing construction and resulting delays, the successful deployment at this site set a strong foundation for future rollouts. The success of this initial implementation generated confidence and led to requests for additional training and configuration support. These preparatory efforts ensured that the subsequent launches at the remaining three plants were executed smoothly, with each plant becoming fully operational within two months. Remarkably, the transition from the old system to HiFlow was completed within a week at each location.
During the second go-live phase, we identified a need to adjust the product labeling workflow between post-production and pre-shipping stages. This change was essential to better track pallet weights and provide accurate information for transportation scheduling. HiFlow’s ability to quickly pivot and implement the necessary changes underscored their flexibility and commitment to meeting our specific needs. This adaptability was crucial to the project’s success and ensured that our shipping processes were optimized for accuracy and efficiency.
The integration of our previously external estimating system into HiFlow’s ecosystem was a game-changer. The comprehensive Estimating modules now link directly to pertinent areas like inventory, die and tool availability, scheduling, and purchasing in real time. This integration not only streamlined our processes but also enhanced our ability to respond quickly to changes in demand, production capacity, and material availability. The seamless interaction between these modules has eliminated the inefficiencies of our previous system, leading to more accurate estimates, better resource management, and a smoother overall operation.
HiFlow’s tailored approach, from initial configuration to phased implementation, and their ability to integrate disparate tools into a cohesive system, played a pivotal role in overcoming our challenges. Their ongoing support and flexibility ensured that our operations not only met but exceeded expectations, setting a new standard for efficiency and productivity across all our plants.
Takeaways
Close cooperation during implementation
Another key element of HiFlow’s approach that we greatly appreciated was the close and constant cooperation from their implementation team. Regular communication, facilitated through weekly meetings—sometimes more frequent—kept the project on track and ensured that no detail was overlooked. This consistent dialogue allowed both teams to stay aligned, address challenges promptly, and make necessary adjustments in real time. HiFlow’s proactive communication strategy played a significant role in maintaining momentum and fostering a collaborative atmosphere throughout the project.
The Go-Live phase was particularly crucial, and having the HiFlow team present on-site proved invaluable. Their presence allowed for immediate guidance and troubleshooting, ensuring that our team could effectively navigate the new software from day one. Additionally, HiFlow provided us with a comprehensive library of video training guides, which has become a valuable resource for both current and new staff members. These guides, coupled with printed single-sheet instructions for specific operator tasks, have ensured that our team has the necessary tools and resources to operate efficiently and confidently.
HiFlow’s structured approach to the implementation process, coupled with continuous collaboration and adaptability, was central to the success of the project. Their ability to adjust to on-the-ground realities and respond to the evolving needs of our operations ensured that the implementation was not only successful but also seamless. This structured yet flexible approach instilled confidence in our personnel and facilitated a smooth transition across all our plants.
As a result, the collaboration with HiFlow not only met but exceeded our expectations, setting the stage for continued success and operational excellence. Their thorough understanding of our business, unwavering support during the Go-Live phase, and commitment to continuous improvement have made them an invaluable partner in our journey toward enhanced efficiency and productivity.

Ongoing Support and Continued Partnership
One of the standout aspects of working with HiFlow has been their commitment to maintaining close communication with us even after the implementation phase was completed. This ongoing relationship has been crucial in ensuring that our system continues to operate smoothly and that any emerging needs are promptly addressed. We have continued with regular meetings, allowing us to stay aligned on any updates, enhancements, or adjustments needed as our operations evolve. We rely on HiFlow’s tech support services daily, which has become an integral part of our workflow.
We have been very happy with the level of support we’ve been receiving from HiFlow. The team is not only highly accessible and responsive, but they also provide support throughout the entire business day, which has been incredibly valuable to us. What sets HiFlow’s support apart is their approach—rather than just offering basic tech support, they provide what we would categorize as “how-to support.” This means that they go beyond merely fixing issues; they actively guide us through processes, helping us fully understand and leverage the software’s capabilities.
Knowing that live support is available whenever we need it gives us peace of mind and allows our team to focus on our core tasks without worrying about potential technical hiccups. HiFlow’s support team has consistently demonstrated a positive, solution-oriented attitude, which has only strengthened our confidence in their system and services.
Building Trust Through Consistent Communication
From the very beginning of the implementation process, our team was consistently impressed by the level of communication provided by HiFlow. Regular updates and clear, ongoing dialogue ensured that every aspect of the project was carefully managed and that no detail was overlooked. This consistent communication played a significant role in building trust and confidence in the new system among our team members. As a result, the transition to the new system was smoother than anticipated, and widespread adoption across our organization happened much sooner than we expected.
The quality of HiFlow’s implementation support staff and developers stood out as one of the most valuable aspects of our partnership. “The best part of HiFlow is the implementation support staff and developers. They have been very professional, responsive, and enjoyable to work with,” states Taylor. This professionalism, combined with their responsiveness to our needs, made the implementation process not just successful but also a positive and collaborative experience for everyone involved.
The regular meetings—often more than once a week—were crucial in keeping our team aligned and on track. These sessions ensured that every question was answered, every concern was addressed, and every detail was managed with care. This level of structured communication was instrumental in achieving the project’s goals and in fostering a sense of confidence and enthusiasm among our users.
Thanks to HiFlow’s dedication and the open lines of communication, our team felt supported throughout the entire process, leading to a seamless implementation and a quick ramp-up to full usage of the system across our organization.
Image source: Badger Paperboards
The Benefits of Partnering
with HiFlow Solutions
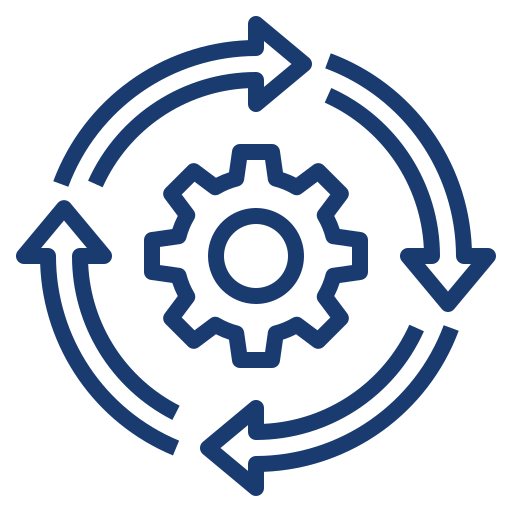
We implement – fast. The HiFlow system combines MIS and MES software with easy ERP integration.

We fill your ERP gaps. By optimizing ERP systems with MIS and MES features required for packaging and label printing.
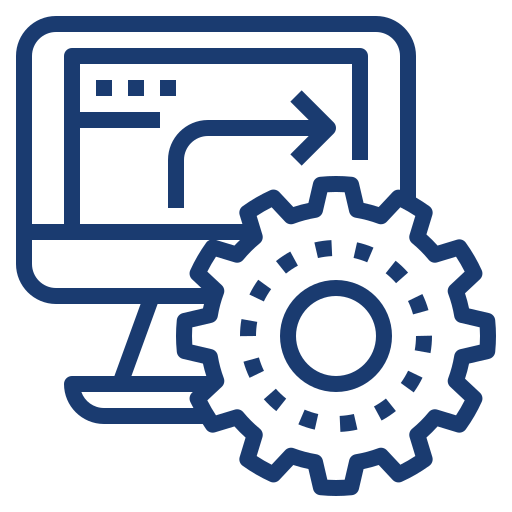
We create automated environments. With seamless connections from order intake to shipping and invoicing.
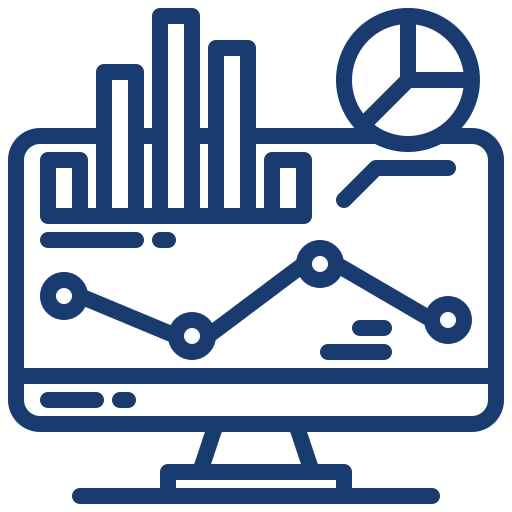
We feed you data. With insights from real time, critical information from your production shop floor, personnel, and equipment.
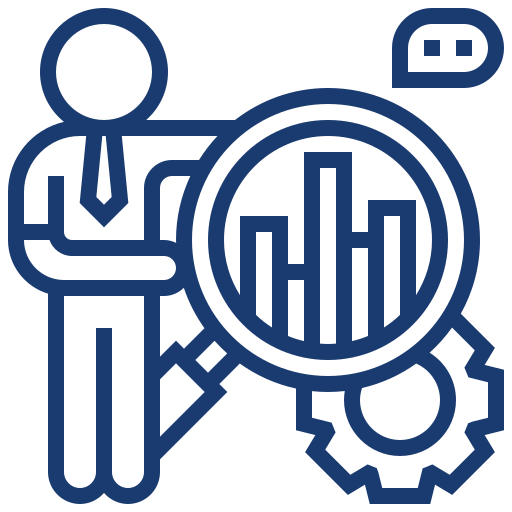
We let you see. From smart scheduling to nested layouts to workflow diagrams, instantly see where you stand within the job.